1) Safety Performance Improvement – Corus Steel Works , Redcar North East England
Results:
- 50% reduction in recordable injury rates over a 12 month period to Corus & contractor employees
Project Overview : As part of the Corus drive to improve safety performance BWC worked with Corus at their Teesside Site over a 12-month period. The project initially focused on changing beliefs and expectations and then on the deployment of a variety of tools such as an Audit-4-Zero system; new root cause analysis techniques and different approaches to induction and permit to work. These were cascaded top down through the organisation via mentoring / coaching out in the workplace in order to really change behaviours. This resulted in some impressive reductions to injury levels.
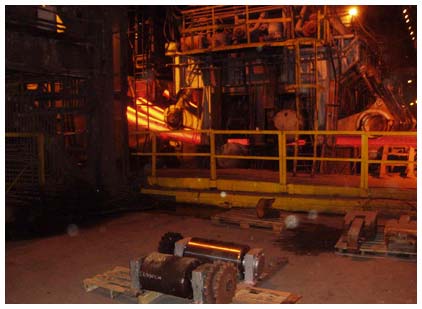
"At Corus safety is a number one priority, and we are always looking to make improvements to our safety performance. We were pleased to adopt the BWC System as it presented us with a fresh perspective on employee safety monitoring and injury investigations."
- David Mulligan, Corus Teesside Environment, Health and Safety Manager